一种离散型钢轨表面缺陷铝热焊缝修复新工艺
发布日期:2008年12月3日暂无评论
在车流中形成的孤立轨头缺陷,无论是通过目测还是超声波探伤检测,如果管理不当,都会显著降低轨头的使用寿命。从网络铁路(NR)基础设施中移除的所有缺陷中,表面引发的缺陷约占50%。这些主要由滚动接触疲劳和车轮烧伤引起的深蹲,这些深蹲是由于在加速转换过程中,由于局部过热导致表面剥落和开裂,轨道和车轮之间的摩擦引入到轨道表面的热量引起的。
在车流中形成的孤立轨头缺陷,无论是通过目测还是超声波探伤检测,如果管理不当,都会显著降低轨头的使用寿命。从网络铁路(NR)基础设施中移除的所有缺陷中,表面引发的缺陷约占50%。这些主要由滚动接触疲劳和车轮烧伤引起的深蹲,这些深蹲是由于在加速转换过程中,由于局部过热导致表面剥落和开裂,轨道和车轮之间的摩擦引入到轨道表面的热量引起的。
在车流中形成的孤立轨头缺陷,无论是通过目测还是超声波探伤检测,如果管理不当,都会显著降低轨头的使用寿命。
从网络铁路(NR)基础设施中移除的所有缺陷中,表面引发的缺陷约占50%。这些主要由滚动接触疲劳和车轮烧伤引起的深蹲,这些深蹲是由于在加速转换过程中,由于局部过热导致表面剥落和开裂,轨道和车轮之间的摩擦引入到轨道表面的热量引起的。
目前,这些缺陷是通过重栏杆或人工金属电弧(MMA)焊接来消除的。这两种方法都很耗时,重铸钢轨通常需要恢复无应力温度,而MMA修复容易引入更多缺陷,如夹杂渣和止/启动气孔。
为了满足改善轨道可用性、减少轨道进入机会和降低维护成本的需求,他们寻求了创新的解决方案,以更有效的方式消除缺陷。
预计HRW工艺可以成功应用于5000 ~ 6000个,占所有隔离表面缺陷的60 ~ 70%。
与NR一起,Thermit Welding (GB) Ltd (TWGB)开发了一种铝热焊接修复工艺,用于修复这些缺陷。
该工艺的设计涵盖了从54(109和110磅)到60公斤/米的220(700)和260(900)等级的铁路段。
背景
最初,TWGB与BR Research和土木工程总监合作,开始开发铝热封头修复焊缝。由于焊接完整性的问题,部分开发被暂停,但主要是因为需要在交通之间进行维修的战略限制。由于现在所有的铝热焊接都是在完整的轨道上进行的,因此人们对该工艺的兴趣重新得到了恢复,因为该工艺比MMA修复或去除含有缺陷的短长度轨道并更换焊接的封闭轨道所提供的生产率和可靠性优势。
该工艺的开发特别注意最小化成本,并尽可能将方法与英国常用的常规SkV-E焊接工艺的设备和焊接实践相匹配。
NR需要一种快速、可靠的修复方法,使其具有与母轨相似的硬度和磨损性能。完成的修复还必须使用传统的行人和火车超声波程序进行完全测试。
通过成功采纳这些目标,NR和TWGB制定了人权观察,包括:
- 通过氧燃料气割和磨削快速去除缺陷
- 常规低压预热-标准SkV-E参数
- 一次性坩埚
- 标准NR批准Thermit部分
- 常规热焊、修边和型材磨削实践
- 采用尽可能多的标准焊接设备
该工艺是传统MMA修复的快速、经济的替代方案,可以在正常的焊接轮班内进行多次修复。
该工艺还可以消除重大的表面缺陷,而不需要安装一个短的封闭轨道,需要两个标准的铝热焊接,并重新施加应力以达到所需的无应力温度。
由于传统的钢轨焊接可能会导致轻微的对准偏差或头部或侧磨损不匹配,因此在安装封闭钢轨时需要考虑到这一点,因此改进的对准方法还可以获得更多的好处。
英国的试验开始于苏格兰的有限数量的缺陷,这突出了一个小缺陷的易感,特别是在早期预浇筑铁路。修正了工艺流程,延长了预热时间,以提高钢轨与焊缝之间的熔合水平。这大大提高了融合水平,并消除了初始试验中出现的小缺陷。
在试验的同时,还为现有的焊工和无损检测(NDT)人员编写了培训材料,使他们能够进行修复过程并进行最后的焊接检查。
全国范围内的试验现已开始,并制定了一项计划,再安装250个焊缝以进行进一步评估。然后,这些试验的结果将用于最大限度地提高适用性,优化修复工艺,并确定可能需要的焊接后无损检测水平,从而全面接受在全国广泛使用。
修复方法
下面给出了HRW范围的细节,以及该过程可修复的缺陷的尺寸(如图A所示)。
人权观察过程各阶段的典型时间安排如表1所示。
准备
缺陷中心的准确位置对于有效去除至关重要:
超声检测使用0°探头建立并记录缺陷长度(包括缺陷可见长度),使用70º探头建立并记录缺陷深度。缺陷的长度和中心使用半永久(油漆)背景上的划线清楚地标记在导轨头的现场一侧。
超声检测用于记录:
- 轨头深度
- 钢轨轮廓和材料等级
- 跟踪类型;S&C,直线
- 每个缺陷的类型和大小,缺陷的数量和每个缺陷之间的距离
- 组件类型;平轨,电弧修复或闪光对接焊接
如果要交付全部利益,检查的准确性是至关重要的。
在轨道上标记待修复区域,并使用专门设计的氧气燃料气割模板和火炬进行挖掘。
可修复的缺陷区域大小:
- 全封头宽度
- 长度可达70mm(额外研磨后可达95mm)
- 深度可达35mm(视轨头磨损情况而定)
对火焰切割表面进行研磨,以准备磁粉检测的NDT表面。如果仍然检测到裂缝,可以扩大到最大允许的尺寸。如果在开挖后仍有任何无法磨除的裂缝,则继续进行修复过程,并由焊工报告修复有缺陷,安装应急夹具并对焊缝进行NDT。如果随后报告焊缝没有缺陷,则无需采取进一步措施即可拆除夹具,或者如果仍然发现缺陷,则使用常规封闭导轨进行修复。
最后的挖掘- 75至95毫米长。
铁路对齐
从维修两侧的两个枕木上拆卸导轨紧固件。校准装置或楔形用于提高维修区域,使轨道参照1米直尺的尖口边缘被提升。
线速度<100英里/小时:提升= 0.5毫米/ 1.0米。线速度>100mph:升力= 1.0mm / 1.0m,见图4。
焊接设备的组装
大多数设备与用于标准SkV-E铝热工艺的设备相同。轨道从修理区域两侧的紧固件上释放出来,并使用楔子升起,在1米的跨度内产生0.5 - 1.0mm的中央升力。安装标准通用安装和预热器安装,并检查预热器高度。
预热器高度:高于开挖中心70mm。
HRW模具检查适合-轻微的调整可能会使适应头部磨损-并插入他们的鞋子。模具密封在钢轨与传统的鲁特材料。
通过维修测试中央芯塞是否合适并放置。
预热
除了特殊的HRW预热器外,该工艺还使用标准的预热设备和常规的SkV氧丙烷预设定压力:
- 氧气:3.0巴,丙烷:0.7巴
- 预热时间:3.0分钟
焊接
预热完成后,移除燃烧器,安装插头,一次性使用坩埚(SUC),预充Thermit®部分位于模具鞋上的定位钉之间并点燃。反应完成后,Thermit钢自动排放到模具中。
凝固和型材精加工
焊接修复冷却6.5分钟,之后使用铝热焊接修剪器去除多余的材料。至少30分钟后,将钢轨固定,并将修整过的表面磨成轮廓。
技术规范
为了全面评估Thermit®HRW工艺的可靠性和效益,NR公司已批准Thermit®HRW工艺进行有限的试验安装。作为工艺测试最初开发的一部分,已对焊缝进行了射线照相和超声波检查,以证明原始缺陷已被清除,且修复焊缝无缺陷。
焊缝冶金和硬度
焊缝的耐磨性受焊缝硬度和热影响区(HAZ)变化的影响。
HRW工艺使用标准焊接部分,并在运行表面产生狭窄的HAZ,这有助于最大限度地减少如表2所示的优先磨损。
强度(弯曲试验)
HRW焊缝三点慢弯试验结果如表3所示,头部在1.0m中心之间受拉。
最终轮廓评估和校准公差
在最终检查之前,应将焊缝研磨到成品型材,最终检查应使用1米的直尺进行,以修复中心。成品型材应符合表4所示公差。用200mm直尺和塞尺检查焊缝表面的平整度。运行面与200mm直尺之间的最大间隙应小于0.2mm。用1米直尺沿运行边缘测量的最大间隙应为+/- 0.5mm。
超声波检查
我们研究了当前的超声波检测程序如何响应修复。NR已对完成的地面维修进行了超声波检查,以确定用于行人超声波检查的Sperry滚轮搜索单元和超声波测试列车的结果响应。试验表明,可以保持完整的钢轨底部回声,这表明焊缝修复对超声波是透明的。使用专门开发的程序进行了进一步的测试,使用手0度、45度和70度探头,以确定超声波测试如何对修复体内部和下方的缺陷作出反应。我们还进行了广泛的测试,以确保修复的相对粗糙的颗粒结构不会掩盖任何剩余或发展裂缝的存在。试件在代表实际缺陷的修复焊缝下钻有特定尺寸的孔。随后对这些样品的超声检查表明,钻孔可以通过修复焊缝金属准确地确定尺寸。修订后的U18超声波程序已经开发出来,用于对安装后的焊缝修复进行详细的检查和评估。
未来的发展
TWGB继续开发HRW工艺,为禁止使用丙烷燃料的隧道/密闭区域提供氧-乙炔替代预热程序。这一程序的初步试验取得了令人鼓舞的结果,希望不久将获得正式批准。
目前正在进行额外的工作,以增加可以通过重叠修复来消除的缺陷的长度。
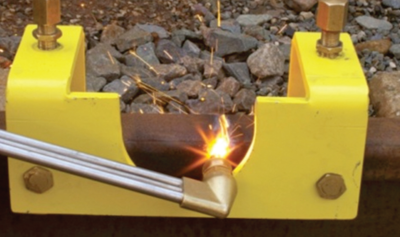
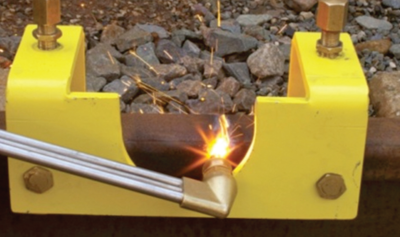
图1:掘进的氧燃料气割
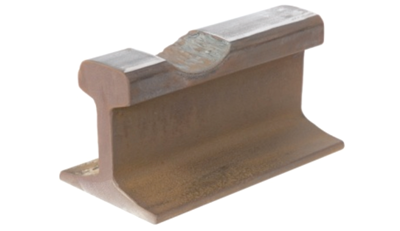
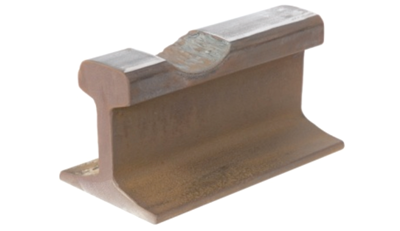
图2:完成的火焰切割挖掘
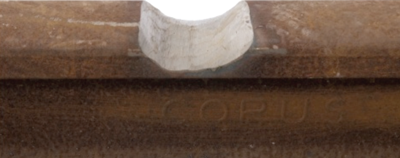
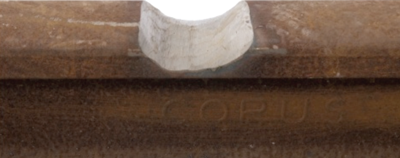
图3:完成地面开挖
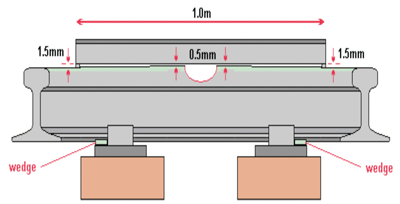
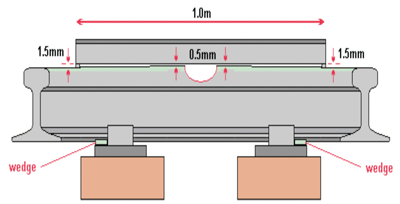
图4:焊接前的导轨对准和升降
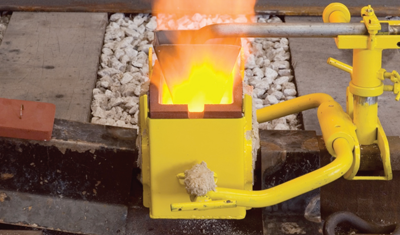
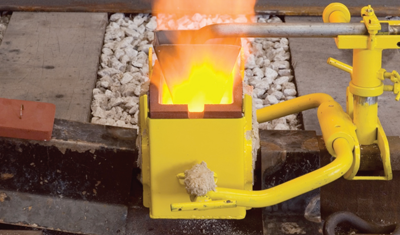
图5:HRW安装过程中的预热
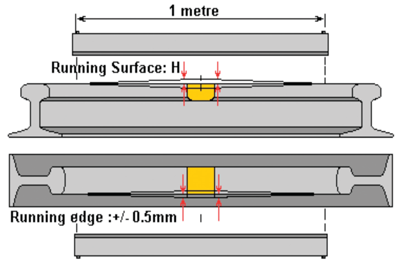
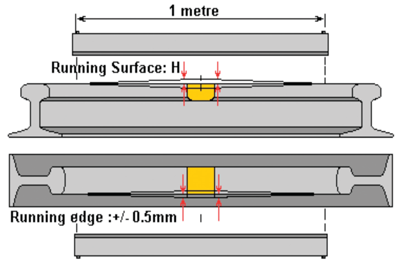
图6:最终钢轨轮廓公差